CAPABILITY
- Home
- CAPABILITY
QUALITY CONTROL
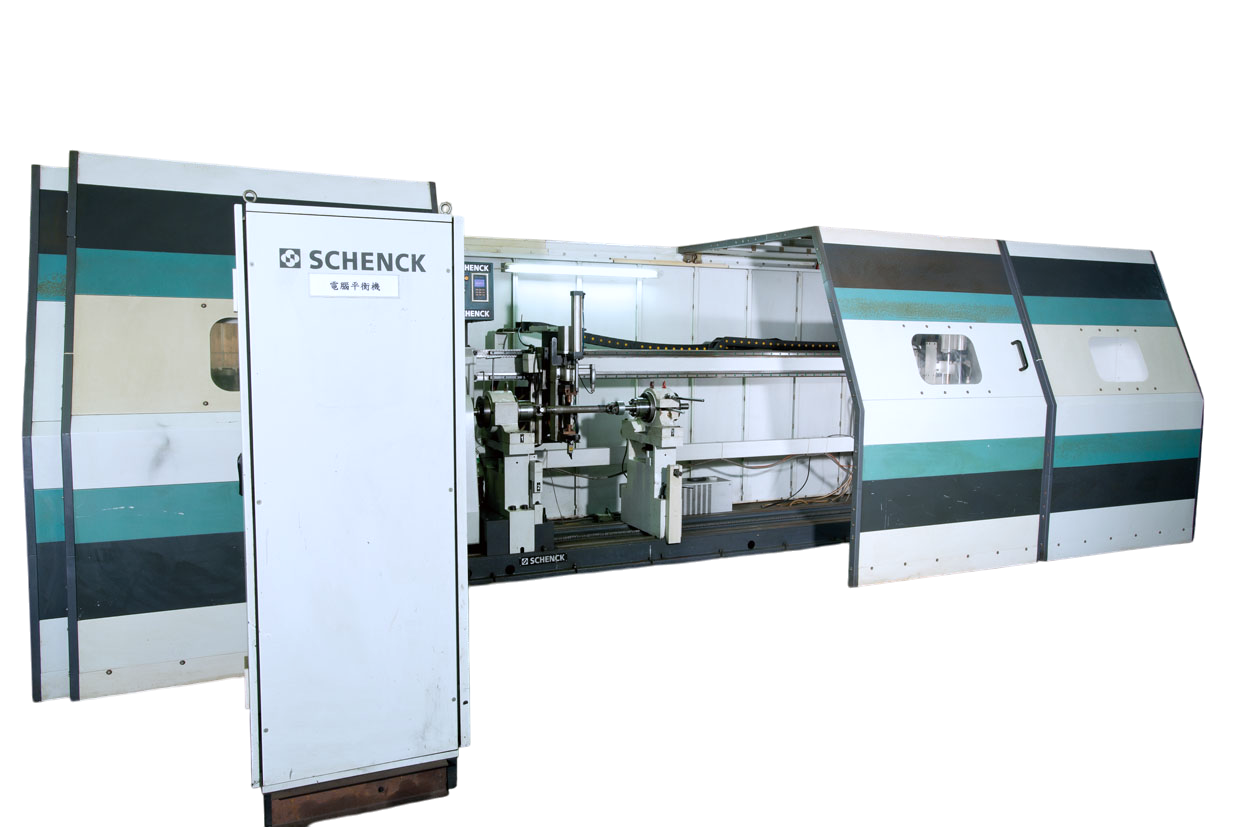
Schenck balance tester
Yi-Jeong utilizes a Schenck Balance Tester from Germany—the only unit of its kind in Taiwan. This advanced equipment supports shafts up to 300 kg and 5.5 meters, enabling high-precision dynamic balancing. Proper balancing significantly reduces vibration, enhances driving safety, and extends the life of both the driveshaft and nearby components. With this system, we deliver consistently balanced shafts for smooth and dependable operation across various applications.
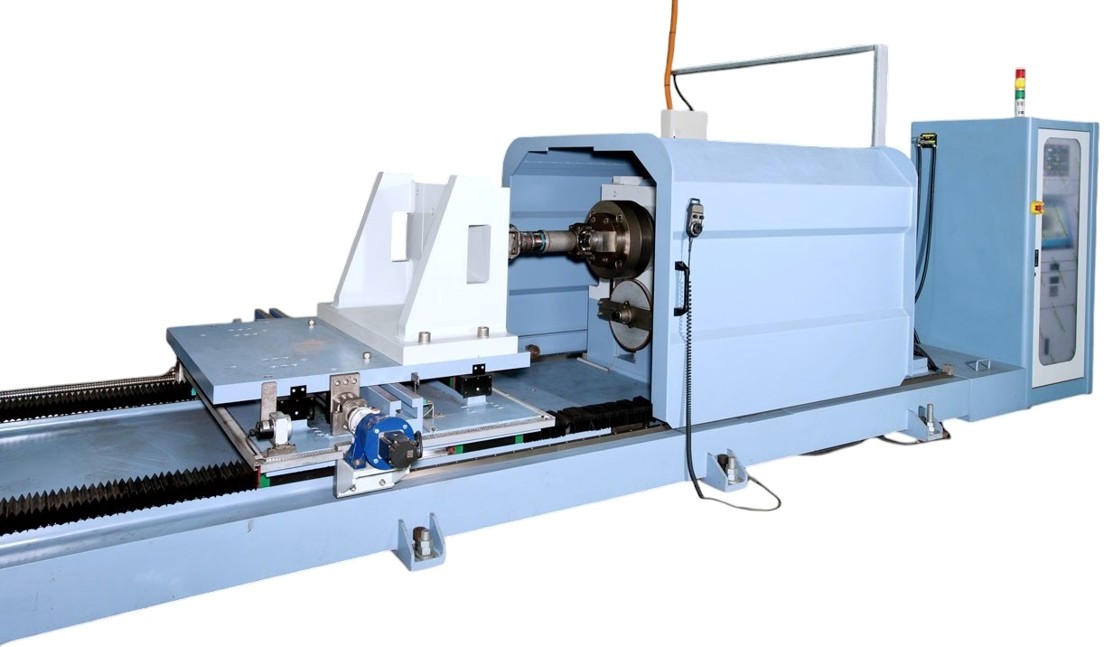
Torque tester
Our torque testing system features Taiwan’s largest capacity and longest testing length. It measures operational and peak torque to validate product strength under simulated conditions. These insights help optimize torque settings and ensure the long-term reliability of each component before delivery.
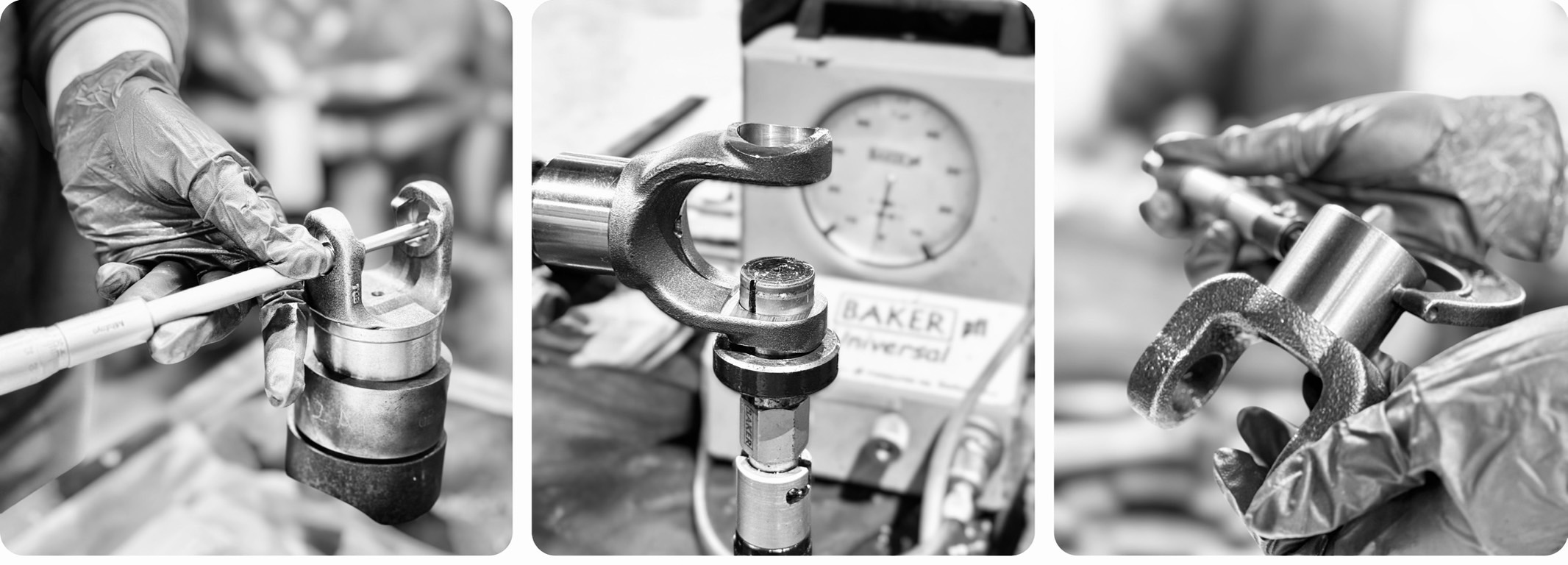
Routine inspection
At Yi-Jeong, our reputation is built on product integrity and consistent quality. Our inspection team conducts regular checks across production lines, validating that each finished component aligns with both the original samples and technical drawings. These ongoing inspections help prevent failures, ensure design compliance, and uphold our commitment to high manufacturing standards.
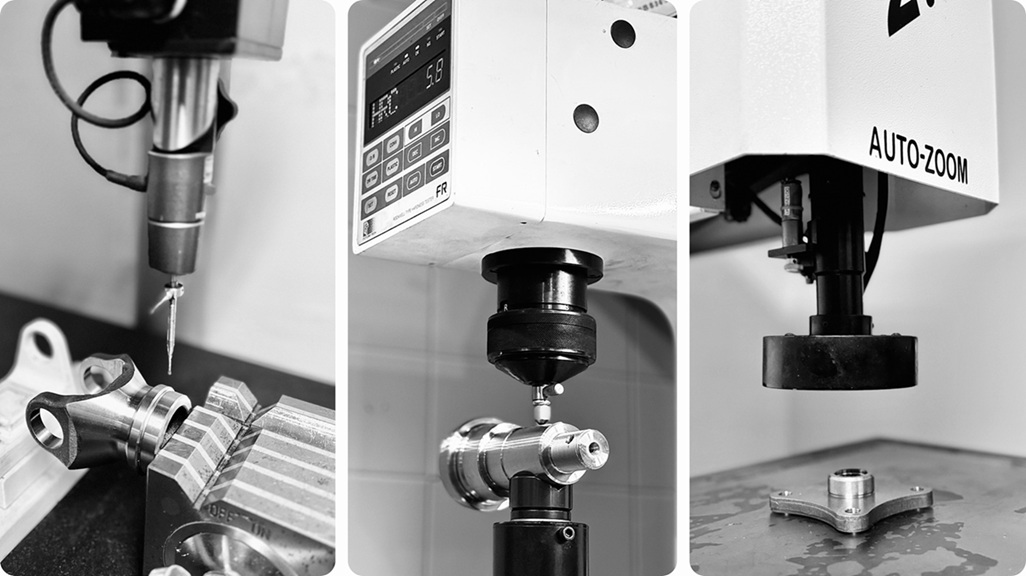
Mechanical testing device
Our in-house mechanical testing lab enhances our ability to validate structural performance before and after production. This capability ensures component consistency, enables prompt technical responses, and reinforces long-term reliability for every shipment.
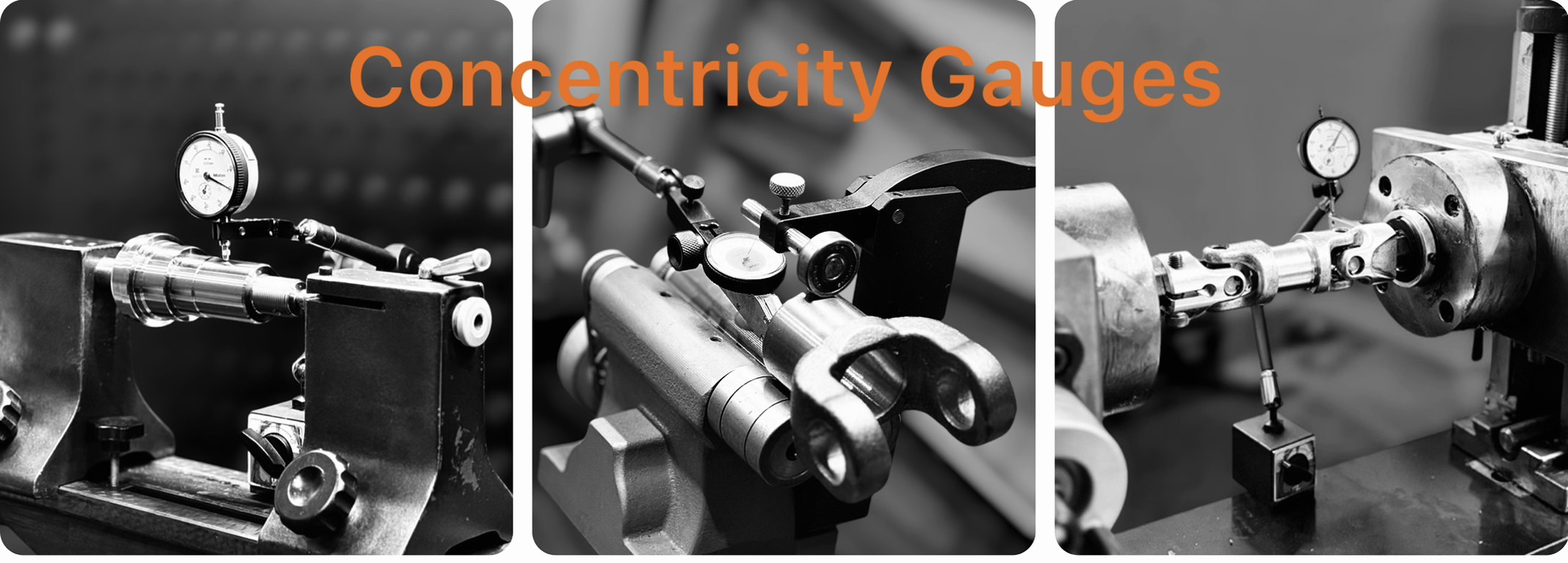
R&D
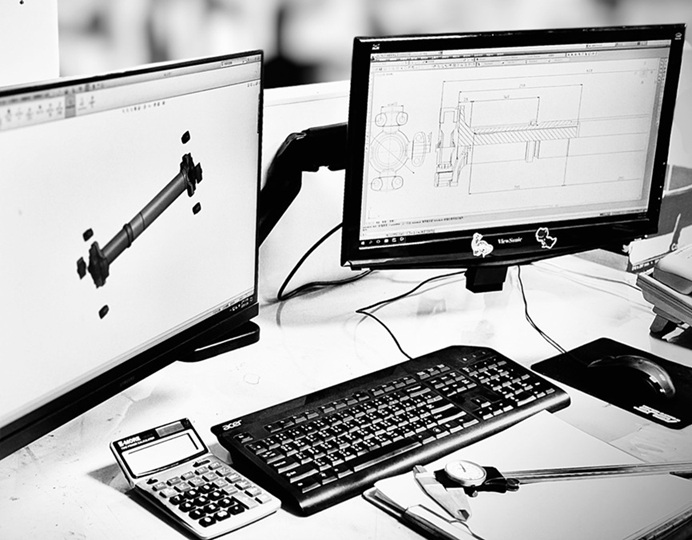
Strong engineering
With more than 40 years of expertise in driveshaft manufacturing, Yi-Jeong combines advanced industrial capabilities with practical engineering know-how. Our R&D professionals work directly with clients to co-develop tailored solutions and provide expert recommendations that enhance product performance and manufacturability.
Prototyping
Yi-Jeong provides both material samples and rapid prototyping through 3D printing technology. These prototypes allow our customers to verify part fitment and make adjustments early—before mass production—minimizing risks and shortening development timelines. Our prototyping services help streamline product validation while supporting high-precision engineering across applications.
Manufacturing
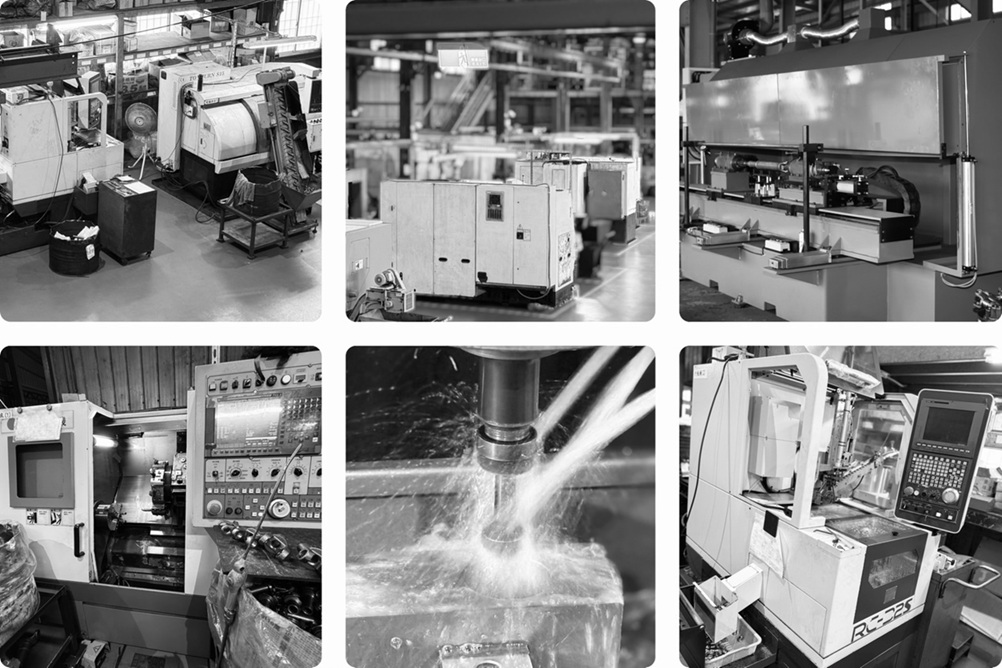
Manufacturing Capabilities
Yi-Jeong is a comprehensive ODM and OEM manufacturer for complete driveshaft systems—not just aftermarket components. From reverse engineering to full product development, our in-house production systems allow for tight quality control and precise delivery management across every stage of the manufacturing process.
✅ In-House Precision Machining: All key machining processes are completed within our own factory.
✅ Strategic Outsourcing: Forging, heat treatment, and large-scale painting are outsourced to specialized partners.
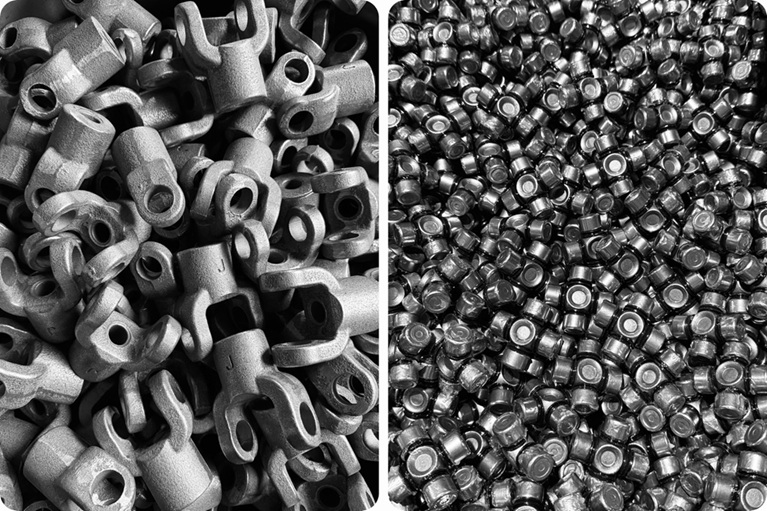
Manufacturing Process
1. Raw Material Processing – We use 100% Taiwan-sourced materials to ensure product consistency and traceability. (Forging, casting, aluminum alloys, etc.)
2. Initial Machining – Rough drilling is performed to prepare components for precision machining.
3. Heat Treatment – Quenching, tempering, or induction hardening (outsourced) is applied to enhance material strength and wear resistance.
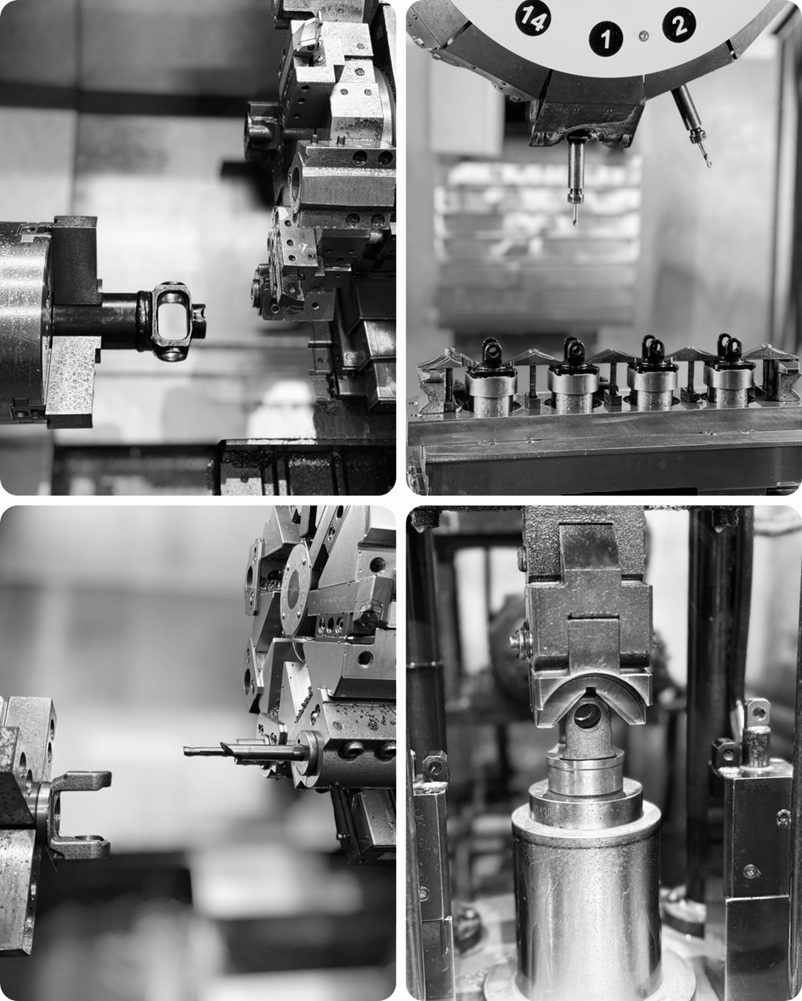
4. Precision Machining (All completed in-house at Yi-Jeong)
✅ Lathing – High-precision turning ensures dimensional accuracy.
✅ Grinding – Achieves superior surface finish and tight tolerances.
✅Hobbing – Precision gear cutting ensures optimal meshing performance.
✅Broaching – Internal spline and complex profile machining guarantee a perfect fit for driveshaft components.
✅ 4-Axis CNC Machining (Designed for Custom Production) – Our specialized 4-axis machining centers integrate multiple processes within a single setup, significantly reducing production cycles and enhancing flexibility for small-batch custom orders.
✅ Tapping – Precise threading ensures secure assembly.
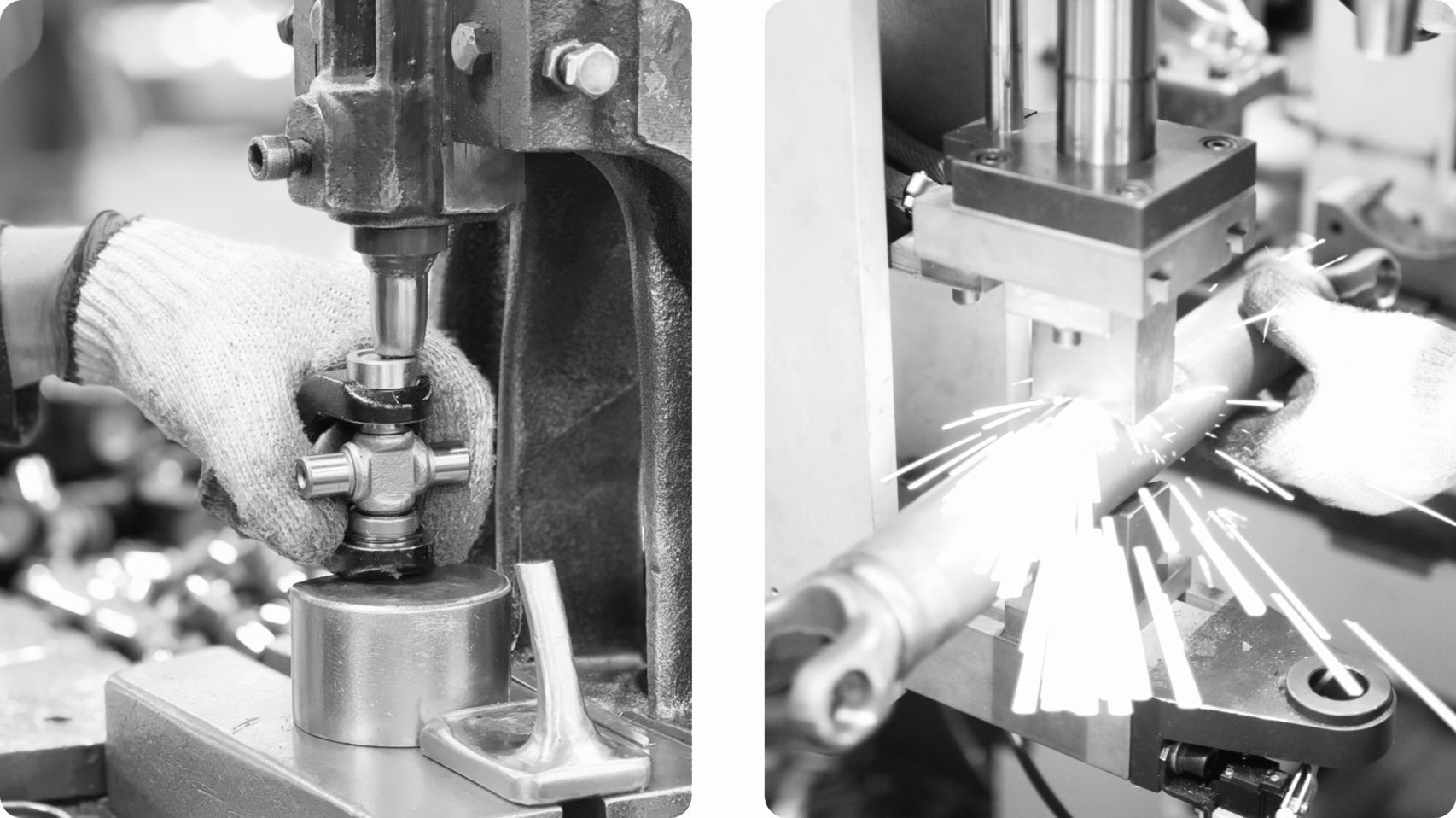
5. Teflon Coating – Applied to tube shafts & midship tube shaft to enhance surface durability, reduce friction, and improve corrosion resistance.
6. Welding & Assembly – High-strength welding techniques ensure structural integrity and durability.

7. Surface Treatment
✅ We have our own in-house painting facilities, allowing us to handle low-volume, high-mix, or urgent orders, ensuring fast turnaround and stable quality.
✅ Large-scale painting is outsourced to specialized partners to ensure high-quality coatings that meet industry standards.
✅ Laser Marking – We offer laser engraving for enhanced product identification and traceability after surface treatment.